MTU Aero Engines sees good progress being made by the EUMET consortium towards its goal of developing a new military engine for the New Generation Fighter (NGF) being developed by France, Germany and Spain and has proposed two initial powerplant concepts.
Part of the overarching tri-national Future Combat Air System (FCAS) programme, the calmness at EUMET contrasts sharply with the early stages of the NGF work which were marked by bickering between Airbus Defence & Space and Dassault Aviation over workshare.
Comprising MTU and Safran, with ITP as a partner – representing Germany, France and Spain, respectively – EUMET has already begun working on design concepts for the powerplant, says Michael Schreyogg, chief programme officer at the Munich-based firm.
While noting that specific details of the engine remain classified, Schreyogg says the architectures of the two concepts proposed differ sharply: one is conventional and the other is adaptive, he said at the Dubai air show.
The latter has a “bigger advantage over the conventional [design]”, he says: “I think this will be the eventual configuration to be selected by the customers.”
Equally, no details of the afterburning engine’s proposed power output can be disclosed, but Schreyogg says it its thrust range “goes higher” than that of either the Safran M88 or Eurojet EJ200, respectively powering the Dassault Rafale and Eurofighter Typhoon. The M88 is rated at 16,500lb (71kN)-thrust, while the EJ200 puts out 17,500lb.
Current development activities under EUMET’s Phase 1B contract are focused on technology maturation, including of advanced materials, alongside aircraft integration studies. Power management also continues to be an area of focus given the high energy demands of a sixth-generation combat aircraft.
The current contract runs until April 2026, but Schreyogg is anxious to obtain sign off for the next stage of work, which will cover the development of a ground-test demonstrator.
“We are really pushing that [the nations] get this under contract in 2024,” he says.
With the Dassault-led NGF demonstrator to be powered by the M88, EUMET does not need to deliver prototypes to support flight testing until the 2030s. “That’s when the first prototype engines will be ready,” he says.
Work on the engine is divided equally between the EUMET partners: MTU is responsible for the front section (the fan and low-pressure compressor), Safran the hot section, afterburner and control system, and ITP the low-pressure turbine and nozzle. Safran will also lead the engine’s overall design and integration, while MTU is in charge of service activities.
Meanwhile, MTU and Safran Helicopter Engines (SHE) are progressing their plans to form a new joint venture to develop a next-generation turboshaft engine for military rotorcraft applications.
Revealed at the Paris air show in June, the joint venture will be based at SHE’s headquarters in Pau in southern France, and run by a chief executive from MTU.
Schreyogg hopes to have the joint venture formalised by the turn of the year, including settling on a name.
However, anyone hoping the business will have a snappy brand are likely to be disappointed: “I don’t care too much about the name – I’m happier with the partnership with Safran.”
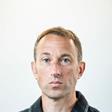