Guy Norris/SEATTLE
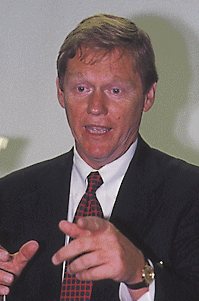
Alan Mulally (left), Boeing Commercial Airplane's president, gestures to a wall festooned with charts, graphs and yellow stickies, and asks: "Does it look familiar to you?" This is the "inside room" across the hallway from Mulally's office - the powerhouse at the core of the company's "better plan" for recovery.
The gallery of graphs records the company's vital statistics: jobs behind schedule, parts shortages, engineering releases, deliveries, forecasts, overtime and employment. In short, everything a president and his staff need to know about the company's direction. Not surprisingly, it bears an uncanny resemblance to the wall in his office at Everett during his days as 777 programme manager. This time, however, Mulally's philosophy has expanded to cover not just a single aircraft programme, but the entire Boeing Commercial Airplane group.
Instead of project engineers and divisional heads, his Monday meetings are attended by the chiefs of the three profit centres created during the radical shake-up which was instituted with the "better plan". Jim Jamieson, head of single-aisle programmes; Jim Morris, his opposite number on Everett's twin-aisle products; and Tom Schick, head of customer services, each come to this room armed with their latest figures. They share the data with Fred Mitchell, who heads Airplane Components. "Mitchell comes in and flows his data up into this," says Mulally. Mitchell, in turn, represents the various discrete disciplines and locations that support the three main profit centres. These include aircraft systems and interiors, fabrications, materials, propulsion, wings and the Tulsa and Wichita organisations.
Mulally's tactics, just like the rest of his plan, are simple. By federating responsibility and allowing the data to be shared openly in this way, he hopes to foster the "working together" attitude which pervaded the 777 effort. This philosophy worked well in the big twinjet's development, but has - up until now - failed to penetrate to the same extent, into other parts of the company. "It is not just one person worrying about how to fix a problem," he says.
Getting results
Re-organising an entire company around a model used to successfully develop an aircraft is one thing; making it work is something else. Yet, according to Mulally, the results show the approach is working. A steadily rising stock price, increasing profit margin and on-time deliveries support his view that the company has more than turned the corner.
"How can you put together more aircraft with fewer people? That's the story right there," says Mulally. "That's why the margins, which is earnings divided by sales as a percentage, go up. Last year we were zero - but by year-end it will be 2% to 3%. We are putting out more aircraft, with fewer people, less overtime and we are doing it where revenues are exceeding costs," he adds.
A scan of the wall gives an idea of how things seem to be looking up. The "health"' of the production system, which catastrophically deteriorated to an all-time low in late 1997, continues its steady improvement as judged by Boeing's metrics. Jobs behind schedule, which dramatically impacted the on-time delivery of aircraft and ultimately the company's entire bottom-line, have shown particular progress.
In October 1997, at the low point in the crisis, these approached 45,100 across the company's commercial product lines. By last month, this tally was down to 9,985 with a year-end target of 4,845 well in sight, says Mulally. Parts shortages, which reflected the upstream impact on Boeing's struggling suppliers, reached a critical 2,600 at the peak of the problems. These are running at around 460 and are projected to be as low as 246 by the end of the year.
Another crucial parameter, the release of engineering drawings to production, is also improving. Labouring in the doldrums at around the 60% level in the middle of the production crisis, they have climbed back to around 90% and the year-end target of 95% has been set with confidence, adds Boeing.
Employment, which was at around 115,900 for BCAG in October 1997, has been one of the most difficult areas to solve, but is also showing an improvement for the company. It rose to 122,900 in July last year while Boeing tackled its short-term production problems by hiring more line workers.
The staff problem was compounded by the temporary absorption of other former Rockwell and McDonnell Douglas sites into BCAG before the latest reorganisation. Employment subsequently fell back to 118,000 by the end of last year and is expected to be around 94,000 by year end.
The bottom line, as far as the airlines are concerned, is on-time deliveries and Boeing's ability to meet demand. Having accomplished the feat of delivering 546 airliners at the end of last year, the company is now aiming at 620 for 1999, including the first 717s. Of the total, 276 are expected to be Next Generation 737s, against 164 last year. The astonishing ramp-up in production to meet demand was partly to blame for the mess in late 1997 - a situation compounded by development issues with the Next Generation aircraft itself. Now the Next Generation line is cranking out 24 aircraft a month, a peacetime record for a large jet-powered aircraft, and 275 are expected to be delivered in 2000.
Target reduction
The overall delivery target for next year has been reduced slightly, from 490 to 480, as a result of the continuing Asian economic crisis. The problems of the region particularly made an impact Boeing's twin-aisle programmes and was the single biggest factor behind the company's decision to drastically cut 747-400 production. Deliveries of the -400, which reached 49 last year, are forecast at 48 this year, before sliding to around 14 in 2000.
This itself is a slight upwards adjustment of the earlier predictions for 2000 which saw both annual production and deliveries (not necessarily the same thing), reduced to as few as 12 aircraft. A rash of recent -400F freighter orders has fuelled speculation that the planned production rate for 2000 may be raised once more in the light of these, and other prospective orders.
The same crisis that hit the main 747 customers also took its toll on the 777. Production of Boeing's biggest twinjet aircraft is due to peak this year with 85 due for delivery, many of them to major US carriers such as American, Delta and United. Deliveries for 2000, however, are expected to be around 55 against the 64 originally scheduled by the long-term order book planners.
The trick, as far as Mulally is concerned, is how to continue the recovery while dealing with the effects of the Asian flu. Mulally believes that the region shows signs of economic recovery, and says the prospect of higher margins in the near future depends on "a soft landing in Asia". His ultimate plan is to reduce the impact of outside events on margin by "working productivity faster than those sales are dropping off".
"Our best shot right now is 480 [deliveries for the year]. We will decide around September, October, November if the deliveries will be up, down or the same." As for guidance on those decisions, Mulally adds: "You have to look at the economics. Look at Asia. Right now, the one that's dominating is Asia.
"We've said we're cautiously optimistic - look at travel around Japan to see it's kind of coming back. If it comes back, then we'll be prepared to go up in production. So we'll just watch it, and we have plans in place, we're getting more efficient. Twelve months away, we'll make a decision. It will happen model-by-model. The 737s are at 24 a month, so the models that will come back mainly are the 747s and 777s. The 777s are still at five a month and the most we've done is seven, so it's not such a big deal."
Productivity, and overall flexibility to alter production rates to meet demand, is being improved slowly but surely by a host of initiatives such as Lean Manufacturing, Make/Buy and DCAC/MRM (Define and Control Airplane Configuration/Manufacturing Resource Management).
Although the introduction of elements of DCAC/MRM was deliberately delayed in the midst of the production crisis, they are being brought to bear throughout Boeing Commercial Airplanes. Other production improvement initiatives such as FAIT/AFA (Fuselage Assembly Integration Team/ Accurate Fuselage Assembly), are also being introduced on lines such as the 747, 757 and 767, with apparent success in cutting assembly time, reducing cost and improving quality.
Many improvements have been made possible because of the digital design techniques introduced with the 777 and perfected on the Next Generation 737 and 757-300 programmes. The result is an increased inertia towards shorter production cycles and dramatically improved response time. "Can you imagine how exciting it will be to make aircraft so they go together like Fisher-Price toys on Christmas Eve?" says Mulally.
The changes are coming just in time to cope with the surge of new models either in early production, flight test, pre-production or final design. "We're really working the productivity and efficiency on those new aircraft: driving down the learning curve. I can't think of a time in our history where this percentage of our total output was relatively new aircraft. Usually, you have one new aircraft, but the rest were established models.
"This time you have the 717, 737-600, -700, -800, -900, BBJ, 757-300, 767-400 and 777-300. So about 70% of the aircraft in our production cycle are relatively new, so we have nowhere to go but up. It's just how fast you work the improvements of putting aircraft together," says Mulally.
Boeing's profit problem has been compounded by the inescapable fact that new aircraft have smaller profit margins. The break-even on the Next Generation 737 was raised to around 800 units after the 1997 problems, but could be lowered before that target is reached, given sufficient progress on the productivity improvement side of the ledger. The far larger margins on mature products, such as the 747-400 and 737 "Classic", on the other hand, have been eroded as the production levels have dropped. The last two 737 Classics are to be delivered in 2000.
New developments
With recovery under way, Boeing's mid-to-long term focus is returning to new product developments: most in the large aircraft arena - the 777-200X/300X and 747 growth, but with some research and development funding earmarked for 757 and 767 programmes. Talk of the Large Airplane Product Development (LAPD) study programme, first revealed in Flight International (24-30 March), remains officially subdued. Boeing says the LAPD study is a way of keeping "in touch" with both the changing technology and market, though the fact that such a study exists at all suggests less than total belief in its own market analysis.
Mulally points to two main trends as evidence that Boeing is right and Airbus wrong when it comes to the big aircraft of the future. He claims that lack of market interest in Boeing's own longer range, higher capacity 747 derivatives is a key indicator of market indifference to the large aircraft concept as a whole, including Airbus' planned 480/660-seat A3XX project. "If we are not getting much interest in a bigger 747, then who wants a big aircraft?" The second argument, and one that Boeing has consistently hammered home, is the continuing phenomenon of fragmentation - the explosion of point-to-point, hub bypass routes operated by smaller capacity twins.
Mulally rejects the argument that the A3XX could create its own market, much the way the outrageously large 747 did 30 years ago. "Why do aircraft create their own market? Because they did something that couldn't be done before. Is the A3XX going to have lower seat mile costs? Based on what I've heard, it is around 8% to 9%, but their goal is 20% and they haven't been able to do it. Check it out: how could you have the same aerodynamics, same engines? How are you going to get 20%? By the number of seats - 700, 800 people? Is it going to fly faster? Fly higher? More utilisation per day? No. Is it going to have longer legs than today? It is just another big aircraft."
The argument of a technology breakthrough, or any other technically-based advantage does not sway him on the point. "Say you're going to make the whole thing out of composites. Breakthrough technology - plastics - say 50% weight savings. Let's look at the operating costs. What's the fuel as a percent of the total? Let's say it uses half the fuel-say it weighs nothing. So you've saved 9% of your operating costs. And 50% of their total operating costs is ownership costs. So if you're going to do something that will really create value in their eyes, you'd have to do something to offer it at a lower cost than a 747 in addition to the improvement that you'd make in operating costs."
The priority for Boeing is the 777-200X/300X series. Delayed by market intransigence, the Asian economic crisis, Boeing's own production problems and the caution of the engine makers, the latest target for an in-service date has slipped back until mid-2003. The early lead Boeing had against the Airbus A340-500/600 series has gone, and Airbus has more than 100 orders in the bag as a result.
"We don't worry about it," says Mulally. "We look at the total market, and it seems like that now we're getting this interest in the long-range 777. What everybody loves is not only that we will have the longest range on the 777-200s but that the -300X will now have more capability than the 747-100s, -200s and -300s. So all of a sudden we've done our original dream of having more efficient replacements for early 747s."
In every argument posed by Boeing, the bottom line appears to be ownership costs. Mulally stubs his finger on the large yellow half-moon of the pie chart that represents cost of ownership and says: "That's what we will be attacking."
With the company quickly turning around, and margins on the rise, it seems hard not to believe him.
Source: Flight International