GKN Aerospace is seeking certification for a new fuel-saving fan blade coating that when applied during the repair process leaves the part “better than the original”.
Tests of the proprietary ceramic coating – an in-house development – have so far shown it can maintain for longer the 1% improvement in specific fuel consumption at engine level achieved by repairing blade leading edges.
Trials of the coating have taken place at the tier one supplier’s newly opened blade repair facility near San Diego in California using a Pratt & Whitney geared turbofan (GTF) engine in partnership with an undisclosed airline. “We have had very good results,” says chief technology officer Russ Dunn.
As the original blades lack a coating, Dunn claims the process means “we are putting fan blades back into service that are better than the original.”
GKN is currently validating the process for the fan blades of several different engines, he adds.
Dunn says the concept sprang from internal research into the “negative effects” of “fan bade degradation in flight”.
“It was actually through that R&D work that they then started to explore different coatings and whether they would provide better [anti-]erosion properties,” he says.
While GKN does not manufacture fan blades itself, GKN chief executive Peter Dilnot sees no reason why it could not licence the technology if it proves sufficiently durable in the long term.
Meanwhile, the company is also closing in on the next additively manufactured component it hopes to bring into series production.
In what it claims was a world first, GKN in late 2023 began making fan case mount rings (FCMR) for PW1500G engines using additive technology.
With around 50% of its PW1500G FCMR output now produced using additive manufacturing, GKN is looking to expand the number of products made this way.
It has identified an initial list comprising “tens of parts”, says Dilnot, across engines from multiple manufacturers.
They include GE Aerospace, a company with which it signed an agreement last year, expanding its risk and reward sharing position on the GEnx powerplant in exchange for pulling “our additive manufacturing into the engine”.
While Dilnot does not specify which components it is targeting, he says “there are a number of GEnx parts on that list”.
But before the additively-made parts can be introduced, regulatory approval is needed. “We have more than one in the certification process at the moment,” adds Dilnot.
GKN sees multiple advantages from additive manufacturing, including potentially lowering the weight and cost of components, alongside improving supply chain resilience through the removal of bottlenecks.
“Why the OEMs and all our partners are knocking the door down is because it’s an alternative to forging and casting in large scale.
“One of the gating factors for the industry at large is the availability in the capacity for cast parts, particularly very large parts.”
While Dilnot says GKN will not be able to take over the entire $30 billion forgings and castings market “if we were able to take 5% of that market… it is going to double the size of our engines business”.
GKN is investing £300 million ($401 million) in additive fabrication technology over the coming years, which by 2029 should generate an additional £50 million in incremental operating profit.
Dilnot says its “modular” concept – the technoogy required is potentially able to fit in a little as two shipping containers – could be installed at or near to a customer facility.
“I think this modular approach, which is the vision here, will ultimately be able to scale up,” he says.
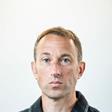