Housed in the lower floor of an otherwise nondescript building in a business park in the English Midlands is a piece of equipment that Collins Aerospace hopes will play a leading role in aviation’s low-carbon future.
Suspended like a museum exhibit in exploded form – its stainless steel parts appear almost polished for display – the object in question is a new 1MW electric motor that is being built to equip a low-emission demonstrator engine, proving out suitable technologies for next-generation powerplants.
Although there is unlikely to be a single energy source for future aircraft – hydrogen, sustainable aviation fuel (SAF) and batteries will all play a role – the common thread linking the different propulsion solutions is the greater use of electrical power.
At the smaller end, electric vertical take-off and landing (eVTOL) aircraft should be able to fly on batteries alone, or use a hybrid-electric powertrain to extend range; hydrogen fuel cells will enable zero-emission regional operations; and even if fuel – be it hydrogen or SAF – still needs to be burnt, a turbofan engine with a boost from an electrical motor – another form of hybrid - will unlock more efficient performance.
But if electricity is to be at the heart of aviation’s sustainable future, then a whole range of new components is necessary to support its application.
Well, not new exactly, after all, electric motors have been around for centuries, even before Tesla – Nikola, that is, not the auto manufacturer – patented his electro-magnetic concept. But to design the high-power motors needed for aerospace applications - plus the motor controllers and high-voltage electrical distribution system to support their operation – is another leap entirely.
But in the quiet commuter town of Solihull, just to the south of Birmingham, aerospace giant RTX is preparing for this electrically driven future, and the 1MW motor on display – completed in early July - is very much part of that vision.
In propulsion terms, RTX is best known for its Pratt & Whitney unit which makes large commercial turbofan engines, but in future, sister company Collins will play an ever more important role in ensuring those engines perform at the highest level, driving down fuel burn and emissions.
The Solihull facility is a centre of excellence for electronic controls and motor systems – one of five sites globally leading the firm’s electrification drive. The site has had a history of developing motors and motor controllers stretching back for the last 30 years, with an $18 million expansion opening in 2018.
In-service products designed and developed at Solihull include the motors and controllers for the Airbus A350’s thrust-reverser system.
The work on the A350, and other programmes before it, encapsulates the message from Phill Godfrey, chief sustainability officer at Collins Aerospace, that the future is not just about electric propulsion, but also more-electric systems – electric actuators replacing their hydraulic or pneumatic equivalents, for instance.
For Collins, that means hybrid-electric powertrains and more-electric systems are part of the same sustainability strand the company calls its “electrified aircraft initiative”.
But to manage that change is no mean feat. “You’ve seen the evolution of aerospace go from demanding very little power to from the aircraft all the way up to where we are today when loads are becoming larger and larger,” says Zubair Baig, senior technical fellow, electrical systems, Pratt & Whitney.
“As we go to more electrical systems, the demand for the aircraft and the power distribution system gets more and more complex.”
Collins is not pursuing these goals alone, of course: an aircraft is essentially a system of systems, therefore cross-industry collaboration is vital. That is exemplified by one of the company’s first electric propulsion projects, which sees it working alongside sister firm Pratt & Whitney, plus airframer De Havilland Canada and battery developer H55, to retrofit a hybrid-electric powertrain onto a Dash 8-100 regional turboprop.
The powertrain for the hybrid-electric flight demonstrator includes a 1MW electric motor and motor controllers – both developed in Solihull, naturally – coupled with a P&W thermal engine.
Around 50% of the power for take-off and climb will come from the electric powertrain, allowing the thermal engine to be right-sized for cruise, improving fuel efficiency by about 30%, says Baig. Ground testing of the demonstrator is ongoing, but it is not clear when the demonstrator will fly this year – the company’s previously stated goal.
Pratt & Whitney Canada says the powertrain has yet to be fitted to the aircraft, although the critical design review milestone for its integration has been passed. “Our current focus is testing the hybrid-electric propulsion system at a Pratt & Whitney Canada test cell facility in Longueuil, Quebec, before installing on the experimental aircraft,” it says.
“We have made significant progress testing the thermal engine and 1 MW motor to their rated power (individually) and are now progressively testing the combined propulsion system towards its full power.”
Nonetheless, the ground-test effort is contributing to RTX’s understanding of what will be required for the single-aisle market, says Baig. That step will be “a little bit more challenging”, he says, which is somewhat of an understatement given that a narrowbody jet will need around 10MW of electrical power to achieve the same 50% level of hybridisation.
“If you are familiar with where technology is today, with batteries and high-voltage systems, that [level of power] is not where we are,” says Baig.
RTX’s roadmap foresees a hybridisation level of around 5% being applied to narrowbody engines in the near-term to address the “key weaknesses” of those powerplants, chiefly the “off-design points” – the parts of a flight for which the engine is not optimised, such as take-off or idle power.
“We want to maximise the efficiency so we utilise the hybridisation as a knob to be able to boost efficiencies in those segments so that we get greater returns,” he says.
A first narrowbody application for those learnings – and a pair of the 1MW electric motors being built at Solihull – will come on a project funded by the EU’s Clean Aviation initiative. Called SWITCH – sustainable water-injecting turbofan comprising hybrid-electrics – the MTU Aero Engines-led research programme marries a donor turbofan, in this case a PW1100G, with the German firm’s steam-injection technology and the Collins electric motors, with a target of cutting fuel burn and CO2 emissions by 25%.
The programme essentially brings together two different – and independent – technologies that could potentially equip a future powerplant: MTU’s Water-Enhanced Turbofan (WET) concept and hybrid-electric power. Of the two parts, the WET engine is the more radical – and challenging – element but with a potentially larger overall benefit. However, while smaller, the efficiency gains from hybridisation are likely more easily realised.
Collins proposes to attach the motors to both the high- and low-pressure spools, respectively locating them on the accessory gearbox and in the tail cone. While both are 1MW units, the motor on the high-speed spool is de-rated to 500kW. And although not identical, they are derived from the 1MW motor built for the Dash 8 conversion.
Baig points out that the current configuration is not production-ready but a design that has mostly been guided by pragmatism. “It’s a learning tool, not necessarily a product,” he says. “Tearing apart an engine is not simple – this is the least disruptive means of getting to where we want to be.”
Funded under Clean Aviation’s Phase 1, the current SWITCH project only stretches to ground testing – due by 2026 – but, says Baig, the ultimate aim is to take the engine to flight, potentially in a follow-on phase. That could also see the incorporation of technologies developed through HECATE, a separate Clean Aviation project led by Collins’ unit in Cork, Ireland that is working on a high-voltage electrical distribution system. HECATE recently passed the preliminary design review milestone, as it moves towards ground tests of a 500kW hybrid-electric system at TRL5 by 2025.
Although there is considerable effort being expended on larger engines – those being the bigger source of emissions to tackle - RTX is not ignoring lower-power applications for hybrid-electric systems either. Through its STEP-Tech demonstrator programme, the company is combining Collins’ electrical expertise with turbogenerators from Pratt & Whitney Canada to focus on developing high-voltage distributed turboelectric hybrid-electric propulsion concepts. Although they are envisaged in the 100-500kW class, there is potential to scale to 1MW and beyond, the company says.
Baig describes the STEP-Tech system as “scalable and adaptable” and is designed to “round out our learnings and our ability to mature technologies and systems in this space”. Individual component tests have been ongoing since last year, with the company recently announcing that it had validated the successful operation of the combined system.
Overall, scalability – of motors, controllers and even entire powertrains – is very much a guiding principle behind the development work.
Josh Parkin, Collins engineering director, electric power systems UK, points to the work on the 1MW electric motor as an example: “We wanted to take on really the most challenging aspect of that and really go for that high power level and then scale back from that depending on what we see our customers are demanding,” says Parkin.
That scalability is already in evidence. RTX is contributing to the hybridisation of the twin-engined H145-based Airbus Helicopters PioneerLab platform. This will combine a derivative of the PW210 turboshaft and a pair of 250kW electric motors - scaled down from the original 1MW design - to replace the platform’s stock Safran Helicopter Engines Arriel 2Es. Meanwhile, the motor controllers for that effort are derived from work carried out on STEP-Tech.
“What RTX brings together is all the experience we have on all those flight demonstrator programmes, technology development programmes that we have been working on, and it will feed into this programme developing these motor controller families, motor families and other technologies we will be testing out on this [PioneerLab platform],” says Kalyani Menon, senior chief engineer, propulsion electrification at Collins.
“RTX really has all the skills and capabilities to go figure out these very complicated, very unique challenges… and to work out how to optimise [them],” says Steven Kotso, executive director, electric propulsion, Collins Aerospace. “Our scalable technology allows to create those building blocks in order to be positioned for whatever system solution the future may need.”
Solihull is also not operating in isolation – its work is supported by research facilities in Cork, Ireland and East Hartford, Connecticut in the USA; the company’s centre of excellence for power distribution in Nordlingen, Germany; and another site Rockford, Illinois. The latter is home to what Collins calls ‘The Grid’, a $50 million integrated system laboratory that opened last year featuring 8MW of test capability, a figure that will eventually rise to 15MW.
“It really shows that RTX has a world-class network of facilities looking at electrification and how we take these technologies forward,” says Parkin.
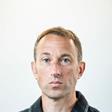