Safran Landing Systems (SLS) is continuing to refine an electric-taxiing system for future narrowbody aircraft that it believes can cut block fuel burn by up to 4%.
Currently in its “third or fourth generation”, the latest version of the eTaxi system is “really responding to what airframe customers are telling us they want”, says Kyle Schmidt, senior vice-president of research, technology, innovation and eco-design at SLS.
Designed for line-fit rather than retrofit installation, the eTaxi unit will be both “removable and optional”, he says. “It has been designed to be integrated from day one, but it doesn’t need to be on every aircraft if the customer doesn’t want it.”
Last decade, Safran developed a prototype system with Honeywell but abandoned the project in 2016. Called the Electric Green Taxiing System, it used electricity generated by the auxiliary power unit to drive electric motors attached to the main landing gear wheels.
Safran proposes a similar architecture for eTaxi, with the “electric taxi actuators” installed on the main gear wheels.
Each actuator contains a high-torque electric motor, a gear-reduction drive, a clutch for engagement and positive disengagement of the system from the wheel, cooling fans, and associated hardware “to operate the system in a convenient and easily mountable/detachable module”, says SLS.
While dependant on the exact aircraft application and performance targets, each actuator can deliver in the range of range 6,000-12,000Nm of torque.
Because the EGTS was being integrated onto in-production aircraft, there was limited potential to optimise the weight and fit of the design.
“By designing eTaxi for a future airplane we can make the interface cleaner,” Schmidt says, while “trying to minimise added weight.”
Although the system is still heavier than a standard wheel, Schmidt is confident the efficiency it brings will compensate for the extra mass, generating a block fuel burn saving in the order of 4%. In addition, emissions of carbon dioxide, nitrous oxides and particulates will all be reduced at the airport.
SLS has taken the eTaxi system to technology readiness level (TRL) 3 or 4, he says, while certain elements are at around TRL5.
An SLS team is “actively working” on the system to bring further improvements, he adds.
“We are working out how we get the system lighter, reduce the parts count and make sure it buys its way on to the airplane a bit better,” he says.
Progress made in the years since EGTS was dropped has seen the system’s weight cut by around 100kg at aircraft level. However, the mass of any production system will be dictated by airframer weight and performance targets.
“We have never stopped internally working on eTaxi,” says Schmidt. “We are firm believers that this brings advantages for operators and airframers.”
Neither Airbus or Boeing has a formal demand for such a system, but SLS is maturing the technology to ensure it could be offered to either airframer as they contemplate replacement of their respective A320neo and 737 Max single-aisles in the 2030s.
Development of the eTaxi is part of a broad suite of R&T activities at SLS – including electrification of the landing gear and the use of lightweight materials – that could find their way on to next-generation aircraft.
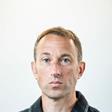