Maturation of an all-new wing designed to deliver a 50% fuel-burn reduction as part of a future hybrid-electric regional aircraft could take place in the second half of the decade if a project led by Airbus Defence & Space proceeds as planned.
Working as part of a consortium called HERWINGT – hybrid electrical regional wing integration novel green technologies – the Spain-based arm of Airbus’s defence unit will test novel materials, configurations and manufacturing techniques that should enable the creation of a lighter, aerodynamically improved wing.
Backed by the EU’s Clean Aviation body with a €21.8 million ($23.8 million) grant as part of its first funding round, the project will by 2025 have matured sufficiently all the required components to allow a full-scale demonstration to take place in a possible second phase.
Antonio Hernandez Martin de Arriva, Clean Aviation chief engineer at Airbus Defence & Space, says the overall fuel-burn reduction goal from the new wing is 50% at aircraft level.
That will be achieved in three ways, he explains: state-of-the-art wing configurations with improved aerodynamics will yield a fuel-burn reduction of 15% at wing-component level; novel structures, better integration of systems and new materials will lower weight by 20%; and lastly, the wing fuel systems will also be compatible with sustainable aviation fuel (SAF).
In addition, by 2025, the project will have produced digital twins and lifecycle assessments of the components, subsystems and full wing, compatible with the project’s reference aircraft, plus a roadmap towards readiness for flight of the new structure, targeting possible service entry in 2035. Certification requirements will also be considered “from the beginning of the project”, adds Hernandez.
Activities under HERWINGT kicked off in February this year, and the consortium partners are now “working on the requirements and configurations of the wing” – a process that includes liaising with other Clean Aviation programmes, notably a Leonardo-led effort called HERA (hybrid-electric regional architecture): “We need to harmonise the wing configurations and wing requirements with the HERA project, where we are defining the requirements at aircraft level,” he says.
Around 15 different component demonstrator projects will inform the final wing design, which will undergo the preliminary design review phase before the middle of 2024, followed by a critical design review in early 2025. “It is a very tight schedule,” notes Hernandez.
That seems an understatement given the number of new technologies, materials and manufacturing processes to be implemented.
Planned “enabling technologies” include new materials such as thermoset, thermoplastic and resin-infused composite allowing weight reduction, and the production of “highly integrated structures” using out-of-autoclave processes. Traditionally composite wings have been restricted to widebody aircraft, with the slow – and expensive – autoclave curing process ill-suited to the high production rates required for single-aisle or regional aircraft applications.
Those new materials or processes will facilitate the development of new wing architectures and more integrated structures which should, says Hernandez , help to “minimise, or even eliminate, the need for joints and bondings” within the wing.
HERWINGT will additionally implement health monitoring systems in the wing, allowing “us to design with less thickness and then less mass”, he says.
Auxiliary systems – for example, induction-based ice protection – will also be integrated into the structure, further reducing weight and drag penalties.
Hernandez says aerodynamic drag will be reduced by the use of a high-aspect-ratio design which uses “morphing control surfaces with optimised flight-control laws, and improved laminarity of the wing”.
Lastly, new sensors, sealants and materials related to the fuel system will be employed, designed to make them compatible with a broad SAF specification.
Also adding to the complexity is the impact on the wing’s design on other parts of the aircraft, such as the fuselage and propulsion system.
In the latter case, even if a ‘typical’ twin-engined configuration is selected there will still be integration challenges from the additional weight and installation constraints such a system imposes.
“Therefore, one of our main goals is to develop new structure concepts and materials for the wing where we can install such new systems minimising the weight penalties within the aerodynamics of the external geometry,” says Hernandez.
Safety considerations are also paramount, he adds, alongside the demands placed on the structure by the high-voltage electrical network, thermal management system and the energy source – be that batteries, fuel cells or hydrogen.
But with a “more disruptive wing configuration”, for instance involving distributed propulsion, “the impact on the structure concept is much higher” and will require “very creative design solutions” to achieve the desired combination of rigidity and light weight, says Hernandez.
“Moreover, the aerodynamics of the distributed propulsion configuration is playing a key role in the optimisation of the wing performances and wing structure weight penalties oriented to the reduction of fuel burn,” he adds.
If selected in Clean Aviation’s second phase, running from 2026, HERWINGT would look to advance the wing as a feasible solution for a twin-motor configuration with expected service entry in 2035.
As yet, any flight testing phase is undefined and will be discussed as part of the phase 2 planning. During the EU’s predecessor Clean Sky 2 programme, Airbus Defence & Space used a modified C295 tactical transport to perform similar evaluations.
Additionally, Hernandez sees the need to evaluate the wing and distributed propulsion system aboard a scaled model prior to any full-size flight-test campaign.
Airbus is conducting other wing-based research projects – Wing of Tomorrow and Extra Performance Wing, for example – which Hernandez says are complementary to the HERWINGT effort through the use of common materials and integrated systems.
However, with those programmes aimed more at the narrowbody, rather than regional, aircraft segment, there is only so much overlap as the respective wings are optimised for different flight conditions.
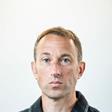