When one company is acquired by another, a period of rapid integration usually occurs as its systems, people and, like as not, way of doing business are subsumed by the new owner, often leaving little more than a name. Yet, sometimes, the reverse is true and the acquiring firm is instead itself transformed by the process.
Such is the case with Melrose Industries, which has fundamentally upended its strategy on the back of its 2018 purchase of GKN plc.
Acting as a “listed private-equity [fund]”, Melrose’s modus operandi was to seek out high-quality but underperforming companies, gain control, turn them around, and then cash out – “buy, improve, sell”, was the tagline of what GKN Aerospace’s chief executive Peter Dilnot calls the “buccaneering business”.
That meant that at the time of its acquisition, GKN – itself four distinct entities, including aerospace – joined a basket of other unrelated companies under Melrose’s ownership. “But that business model is now coming to an end,” says Dilnot.
Just five years ago Melrose had around 10 different operating companies, but a series of divestments had by 2023 left GKN as the only business within its portfolio. Nonetheless, the firm felt it needed to go further.
“It became very clear to us that the business was not trading as it should have in terms of the capital markets in terms of its valuation – the sum of its parts was not adding up,” he says.
With only limited interest from money managers to invest in what was effectively a conglomerate – even one as small as GKN – the decision was taken to carve out the remaining automotive, powder metallurgy and hydrogen units and become what Dilnot calls a “pure-play aerospace business for the long term”. That process was completed last year.
Effectively two brands within the same businesses, GKN and Melrose Industries now exist in parallel: Dilnot is actually chief executive of the latter, having replaced previous GKN Aerospace boss David Paja in March 2024. Along with the new business model comes a new tagline – “design, deliver, improve”.
Dilnot says that in order to grab the attention of the capital markets it was necessary to “shine a light on the quality of GKN Aerospace” and to “describe the engines business, the structures business, the content per aircraft”, alongside financial measures like cash generation and sales margin.
The outcome? “We are now a FTSE 50 business with a total enterprise value of £10 billion [$12.6 billion],” he says. Results last year were also positive: revenue stood at £3.3 billion, up on the £2.9 billion recorded in 2022, while pre-tax profits stood at £331 million, against £62 million a year earlier.
By 2025, GKN’s goal is to be generating £900 million of EBITDA, building on a forecast figure of £710-730 million this year. “It’s a massive step from where we were,” says Dilnot.
STRATEGIC RESHAPING
Thanks to the strategic reshaping, aerospace is “now at the heart of everything we do”, he says. At its core are two divisions operating across the civil and defence segments: aerostructures – which also includes high-voltage electrical distribution systems and transparencies – and engines, also encompassing GKN’s nascent hydrogen- and electric-propulsion interests.
GKN, Dilnot says, is a “rare combination”, being a “super-tier one” supplier where “we think like a peer and act like an OEM” across two areas that elsewhere are rarely handled by the same business.
“Everything we are doing is about improving our position on design… we are not interested in build-to-print [work],” he says. “Our best positions are where we add most value to our customers” – whether that is through risk and reward sharing partnerships with the engine manufacturers, or “deep technology positions with, for example, wings with Airbus”.
But the strategy also means that “we don’t want to play everywhere”. That pivot has already had an impact, with GKN exiting certain contracts in the defence market “which are not favourable or are onerous”.
It has also had an effect on the firm’s footprint, going from around 50 sites at the start of the Covid-19 pandemic in 2020 to a planned 31 by the end of 2025. Some sites have been divested – in April it completed the sale of a structures plant in St Louis, Missouri to Boeing – while others have been closed or merged to create “centres of excellence”.
GKN has also established a network of four Global Technology Centres, the most recent of which is a facility in Dallas Fort Worth, Texas that specialises in additive layer manufacturing (ALM) – or 3D printing.
“What we have got now is a vibrant business with people focused on the right technologies in the right places,” says Dilnot.
Europe – notably the Netherlands, Sweden and the UK – and North America remain the centres of gravity for GKN, with “growing footprints” in India, Mexico and China. GKN now has three sites in China, partly supporting domestic airframer Comac’s production.
Although some of GKN’s growth can be attributed to a buoyant market, the firm’s heavy investment in R&D also has a part to play, argues chief technology officer Russ Dunn. Its spending is focused in four broad areas: additive fabrication, composite technologies, electric flight, and clean-air partnerships.
Technologies supporting hydrogen propulsion are an example of “anticipating the future needs of the market and being ready for what we see coming around the corner”, he says. Research there is exploring what will be required even though “there is no launch platform” for such a propulsion system. “But we know that if we wait until they are ready to launch we will have already missed the boat,” he says.
TRANSFORMATIVE TECHNOLOGY
ALM has been an area where GKN has been pushing particularly hard, seeing it as a transformative technology promising less waste, lower energy use, better component design and shorter supply chains.
This time last year, GKN was preparing to start serial production of a new large 3D-printed part – a fan case mount ring for the Pratt & Whitney PW1500G engine. That operation is now ramping up, and Dunn says GKN is eyeing further applications for the technology.
Expansion of the firm’s ALM capabilities is being aided by a £50 million investment at its plant in Trollhattan, Sweden – including a £12 million contribution from the country’s government. That comes on the back of its October 2020 bolt-on acquisition of Gothenburg, Sweden-based additive manufacturing partner Permanova Lasersystem.
Although Melrose has previously ruled out further large-scale acquisitions, could the quality of assets coming to the market – Rolls-Royce Electrical or parts of Spirit AeroSystems, for instance – tempt the company to loosen its purse strings?
“We shouldn’t rule out M&A completely,” Dilnot says. “I wouldn’t say we’ll do anything material in the next couple of years, but beyond that, if it makes sense, then yes we’ll be open to that. But our bar is quite high on what we would consider.”
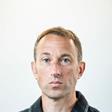