US advanced propulsion system developer Wright Electric has conducted an initial fit check of its WM2500 electric propulsion unit (EPU) related to its potential installation aboard a Lockheed Martin C-130 tactical transport.
Wright has been studying the possibility of using the Hercules as a testbed for its EPUs and, further out, the hybridisation of the platform.
Its interest in the ubiquitous airlifter was spurred by initial research from NASA released last year that suggested significant fuel and emissions savings could be achieved by hydridisation of the aircraft, replacing the outboard Rolls-Royce AE 2100 turboprop engines with 4MW-class electric motors powered by batteries housed in wing-pods.
Performed at an undisclosed US Air Force base on the country’s east coast on 22 January, the check allowed Wright to accurately compare the dimensions of its EPU, coupled to a stock C-130 gearbox, against the nacelle for the AE 2100.
Although a pair of the developmental WM2500s would need to be stacked together to generate sufficient power output “the fit check demonstrated that there is sufficient room in the nacelle for Wright’s EPU”, the company says.
Besides the AE 2100 itself, the conversion to electric power would also see the removal of auxiliary equipment and fuel and hydraulic lines.
“The visit further demonstrates the viability of the Wright EPU being developed with ARPA-E as a viable candidate for hybridisation of the C-130. We are moving from CAD software to real hardware,” says chief technology officer Colin Tschida.
Part of the US Department of Energy, ARPA-E is designed to foster rapid development of early stage technologies and has backed Wright with funding for work on both EPUs and batteries.
Wright’s next focus this year is on the conversion of the wing-pods from fuel to battery storage, running modelling exercises to “demonstrate that we can fill the pod with batteries in a way that fits with its specifications”.
The move comes as NASA has revealed fresh research, examining the potential for a hybrid-electric version of the LM-100J – the out-of-production commercial cargo variant of the C-130J.
Contained in two separate papers presented at the Sci Tech conference at the beginning of January, the studies analyse the feasibility and benefits from an integrated hybrid-electric powertrain on the platform, and the potential market impact from an aircraft with such a propulsion system.
The configuration proposed by NASA for what it calls the Hybrid Electric Turboprop Commercial Freighter (HETCOF) mirrors that of its earlier studies, and that pursued by Wright.
To examine the potential efficiency benefits from a hybrid-electric propulsion system, researchers used the performance of components at three different technology readiness levels.
Although it found that payload would be reduced by around 40% if the configuration used systems at TRL5 and above – those closest to commercial readiness – this falls to parity with the conventional-engined baseline aircraft if the benefits promised by earlier-stage technologies can be realised.
Besides, the hybrid propulsion system delivers key benefits, it adds: “All HETCOF configurations result in increased efficiency and subsequent block fuel, block energy, and block emissions reductions.”
Those benefits “scale with improved electrified aircraft propulsion system performance”, it says. Over a target range of 750nm (1,390km) they deliver: CO2 emissions reduced by 4-10kg per nm, block fuel savings of 27-67%, and block energy savings of 15-35%.
Given those factors, and that the aircraft retains “some or all of the cargo capability of the baseline aircraft across TRL level assumptions”, it would allow the hybrid platform’s “near-term introduction with increasing benefits as technology matures”.
Basing its calculations on a “genericized turboprop freighter” with a 70t maximum take-off weight capable of carrying a 19t payload – roughly the figures listed by Lockheed for the C-130J/LM-100J – the study says using an electric propulsion system at TRL5+ would result in payload falling to 11t.
However, as system weight and power improve at earlier-stage TRL levels so does the available payload, rising to 16t at TRL3-4 and 19t at TRL1-2, the study says.
Designed for regional freight operations, the HETCOF should be capable of serving routes of up to 750nm in all-electric mode and up to 2,400nm in hybrid mode. But achieving those targets “will require substantial technology improvements in energy storage, power system, and thermal systems”, says the study.
For example, electric motors currently at TRL5+ can boast a power-to-weight figure of 15kW/kg, rising to 25kW/kg at TRL3-4 and 50kW/kg at TRL1-2. Similarly, battery performance rises from 250Wh/kg, to 750Wh/kg, and then to 1,500Wh/kg at the same TRL stages, yielding overall battery pack weights of 22t, 9t and 10t, respectively.
However, the report cautions that the “cost requirements” of such an aircraft, particularly a new-build example “are a challenge for initial market penetration”.
Nonetheless, the report notes that “under certain conditions” – high utilisation rates or with elevated jet fuel prices – the total cost of ownership and operation “may be less than converted narrowbody aircraft” currently used for regional freighter routes.
The older airframes typically used for freighter conversions will also be more costly to maintain – potentially twice as much – than a new-build aircraft.
However, “the use of a repurposed aircraft for HETCOF… may be another way to reduce the initial capital cost”, it adds.
Market analysis also “indicates broad market coverage with 73% of the existing mid-sized cargo network within the range of 750nm,” it says.
Analysis of three fuel-burn reduction scenarios – cuts of 30%, 40% and 50% – across a 750nm mission showed the most cost-effectiveness against a converted narrowbody, the study says, suggesting that even if other costs increased the aircraft would remain competitive.
“At the highest fuel reduction scenario [-50%], maintenance costs could increase by 73% (holding purchase price constant) or purchase prices could increase by 37% (holding maintenance costs constant) and the HETCOF would still breakeven,” it notes.
Researchers were drawn from the Volpe National Transportation Systems Center – part of the US Department of Transport, NASA’s Glenn and Ames research facilities, and the ARPA-E programme.
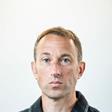