Advanced propulsion developer Wright Electric has begun initial ground runs of its new high-power electric motor as it continues to weigh up which aircraft will serve as a flying testbed for the engine.
Capable of delivering up to 2.5MW, the WM2500 motor has a class-leading power density of around 18-20kW/kg, says Wright founder and chief executive Jeff Engler, a 40% improvement over the 10kW/kg of its previous iteration.
“The goal there is to make it even smaller, even more lightweight, and to try and make it one of the most powerful, if not the most powerful and power-dense aerospace electric machines in the world,” he says.
Initial ground tests of the motor and, separately, the eight custom 250kW inverters required, started recently at Wright’s facility in Albany, New York.
Once a “battery of tests” on both motor and inverters are complete, Wright will combine the separate components for evaluation as a full system.
This will then be shipped to the NASA Electric Aircraft Test (NEAT) facility – located at the agency’s Armstrong research centre in Sandusky, Ohio – where it will be subjected to further trials, including simulated altitude testing.
Engler says partial discharge testing of the previous iteration of the motor at a simulated altitude of 40,000ft was successfully performed, “which gives us confidence to go to NASA’s altitude chamber [with the WM2500]”.
Testing of the WM2500 at NEAT will begin in 2025, potentially running into 2026, before it is transferred back to Albany for additional evaluation on a bespoke test-stand Wright is currently building “and then we go into an aircraft, ground testing, and eventually flight testing”, says Engler.
Should everything proceed to plan, Wright hopes to have the WM2500 in flight test by 2027 or 2028 aboard an as-yet undisclosed platform, leading to certification around the turn of the decade.
Engler says it is “pushing forward” two potential candidates: the BAe 146 regional jet and Lockheed Martin C-130 military airlifter.
While the propulsion system on each aircraft differs – ducted fans versus turboprops – both are four-engined types offering greater redundancy for testing a new motor. In addition, there is “overlap” in their power requirements, respectively 5MW and 3.5MW, in either case necessitating a pair of stacked WM2500s.
Considering two different configurations may also ease eventual commercialisation of the system, says Engler.
“Our customers are always asking us about fan and propeller applications so having two programmes that we are pushing forward gives us some advantage from a data-gathering perspective,” he says.
In either case, for flight-testing, the batteries and turbogenerator would be housed in the fuselage and only one of the four thermal engines replaced with the WM2500 electric motor. Spinning at 7,500rpm, a direct-drive architecture is possible for a ducted-fan design, while a single-stage reduction gearbox is needed to drive a propeller.
Wright has a long-standing interest in the BAe 146 through its ‘Spirit’ programme – first disclosed in 2021 – but development of what was planned as a full-electric aircraft has advanced more slowly than hoped. Under Wright’s initial timeline, the BAe 146 was due to have been flying with one engine replaced by 2023, enabling full electrification by 2026.
Back in 2017, Airbus and Rolls-Royce disclosed similar plans to use the regional jet as a hybridisation testbed under their E-Fan X project – an initiative ditched in 2020 as the pair wrestled with the impact of Covid-19.
Although the pandemic was one reason for the E-Fan X’s cancellation, many observers also questioned the British-built quadjet’s suitability for the mission. Nonetheless, Engler defends Wright’s selection: “Just because a big company decides not to do something, I don’t necessarily take that as a reason for a small company not to do it, as long as one has tried to understand as closely as possible why they made those decisions.”
He insists the type “makes sense as a testbed” albeit concedes it is an “open question” whether a fully hybrid-electric version could become a successful commercial product.
Although Wright’s interest in the BAe 146 stretches back several years, the C-130 has only emerged as a candidate for electrification over the last 12 months.
Spurred by a NASA research paper into the topic, Wright sees a strong potential market for conversion of existing airframes for military customers or civil cargo operators.
A full hybrid-electric powertrain could deliver fuel-burn savings in the order of 27-44%, the research suggested – a welcome boost for cargo operators running on wafer-thin margins – or meet demands from the military for ever-higher levels of on-board power to run sensors, systems and weapons at altitude, says Engler.
He argues an additional advantage of the C-130 is that it has a similar maximum take-off weight as the Boeing 737 – 74t versus 70t for the -800 variant of the single-aisle – “so it gets us squarely into that large regional jet or narrowbody category”.
“And part of what we need to do with the platform, in addition to testing, is build conviction and credibility in the industry that starting to hybridise larger platforms is not just theoretically possible, but actually possible.”
Wright’s ambition has always been to “decarbonise the commercial aerospace industry” and its long-term future hinges on demand for high-power electric motors and batteries from developers of passenger aircraft with 100 and more seats.
But with that point at least five years away, the company’s immediate focus is “how to stay alive long enough to realise our dream”, says Engler.
Other developers have opted to start small, targeting lower-power electric propulsion applications that can be commercialised sooner. But in Wright’s view, the likely change in architecture between a 700kW motor and one in the 2MW class would effectively mean “starting a brand-new programme from scratch”, says Engler, lessening the impact of any saving.
Instead, Wright is targeting component sales to begin generating revenue, notably of its 30kW military-grade generator.
Not aerospace equipment in the truest sense, the lightweight and compact generators – which also double as an aircraft start-cart – fit within the US Air Force’s doctrine of agile combat employment, or the ability to operate from remote airstrips.
Engler argues that as six of its Dynamo generators can fit on a standard 463-litre pallet, against just two standard 30kW generators, the US Air Force can make better use of limited aircraft resources.
Wright has also obtained funding from multiple arms of the US government, including most recently the Federal Aviation Administration, which in August awarded the company $3.34 million to develop ultra-lightweight batteries.
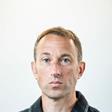