Pratt & Whitney has growing confidence over the potential for a revolutionary hydrogen-combustion, steam-injection turbine engine in the 2050s, after component-level testing of the “hardest parts” of the powerplant demonstrated the feasibility and benefits of the architecture.
Individually, neither hydrogen combustion nor steam injection are new technologies, but P&W’s challenge has been to combine them into a system that can meet aviation’s demanding weight and size constraints, while also cutting greenhouse gas emissions to near-zero.
Under a two-year, US government-backed project, P&W designed, built and tested three critical components – the combustor, condenser and evaporator – for its Hydrogen, Steam-Injected, Intercooled Turbine Engine (HySIITE) concept.
Although hydrogen combustion produces no carbon dioxide or particulates, it results instead in an increase of NOx emissions and water vapour – two contributors to global warming, the latter through contrail formation.
And while steam or water injection is used in the power-generation industry to increase efficiency, P&W engineers needed to find a way of harnessing that technology without the need to “carry thirty, forty thousand litres of water on every flight”, says Neil Terwilliger, technical fellow, advanced concepts, P&W.
The object of the research programme was not to prove that hydrogen could be burnt in an engine, but to answer the question: “How would we design an engine differently if hydrogen was the fuel?”, he adds.
P&W’s concept is, outwardly at least, a conventional geared-fan engine. But rather than simply rejecting the waste heat from the engine core – “useful energy” that would otherwise be lost – it is used to super-heat water in an evaporator to produce steam. This is then injected upstream of the combustor “effectively convecting that waste heat back into the cycle”.
As the evaporator has already cooled the exhaust stream, “it is already getting pretty close to the temperature of condensation” and by feeding it into a series of condensers and a separator, water is produced for circulation back through the system.
The steam-injection process improves the efficiency and power density of the engine and cuts NOx emissions – “essentially driving them to almost zero”, says Dr Michael Winter, chief scientist at P&W parent RTX.
In fact, says the propulsion specialist, the architecture is 35% more energy efficient than the latest-generation PW1100G geared turbofan, has zero carbon dioxide emissions, reduces NOx by 99.3%, and the semi-closed-loop system means potentially less water vapour is emitted than today’s engines.
The NOx result is significantly better than P&W’s initial estimates: when it unveiled the test programme in 2022, it forecast a “more conservative” reduction of around 80% based on the modelling it was able to perform.
For the HySIITE research, P&W built three separate test rigs “focused on the highest risk items”, says Winter, to evaluate the components under simulated operating conditions. That included “putting an evaporator in the exhaust and having it survive”, alongside “demonstrating condensation of water in a sufficient quantity”.
Terwilliger says there was also uncertainty over how effectiveness of the condenser – “whether the water that comes out is going to be microscopic and difficult to capture or if you can just hold a bucket behind it”.
In the event, the tests showed the condenser would be capable of recovering 1.26 litres every second at engine level.
Testing was also needed to validate P&W’s predicted pressure losses through the condenser “because if it was much more, the performance of the whole system may fall apart”.
For the combustor, which used a 0.8 steam-air ratio, P&W sought to “prove that we could do hydrogen combustion in the presence of so much water”.
But the results were positive, showing that hydrogen’s “challenging high flame speed and temperature were effectively tamed by the introduction of the steam”, Terwilliger says.
The evaporator meanwhile, a type of heat exchanger, “has to have high-pressure water and super-heated steam on one side, and sit in the exhaust of a jet engine on the other”.
P&W’s focus, he says, was to “prove we could make it, prove that it lasts in that environment, and that it can successfully evaporate the water and not fall apart”. In the event, “the whole thing held together”, he adds.
Crucially, the testing demonstrated the HySIITE architecture fits within an existing narrowbody nacelle structure.
Plus, while “a bit heavier” than a current GTF engine, the “much smaller core” is lighter and helps to offset the additional weight of the condensers, evaporators and the reserve water needed.
Additionally, because the engine core is significantly smaller, a “pretty extreme” bypass ratio of up to 50:1 can be achieved, says Terwilliger. That compares with a figure of around 13:1 for the PW1100G.
Funding for the initial component development work, which raised them to technology readiness level 3, came through the US Department of Energy’s ARPA-E programme.
Although no dedicated follow-on effort is planned under ARPA-E, “we are looking to continue developing these technologies in a number of opportunities”, he adds.
Terwilliger sees service entry as possible around “2050 not 2030”, if all the remaining hurdles can be cleared.
“There are no shortage of technical challenges. There is no shortage of non-technical challenges. How fast we overcome those is really going to depend on how hard we push,” he says.
“But even pushing as hard as we can, there is still going to be decades or more involved in making this happen.”
Indeed, those non-technical challenges present significant headwinds for hydrogen propulsion: enormous investment is required to produce green hydrogen at scale – not least in massively increasing sustainable electricity generation capacity – and to establish a global storage and distribution network.
Additionally, there will be competition for liquid hydrogen: it is a vital component in the production of power-to-liquid synthetic sustainable aviation fuel (eSAF).
Using eSAF as a baseline, P&W calculated the overall energy savings from instead using hydrogen as a fuel, basing its analysis on hydrogen requiring around 20% less energy to produce than a power-to-liquid fuel, but causing a 15% hit to aircraft energy efficiency due to the larger and heavier fuel tanks needed.
Hydrogen combustion on its own produces only an 8% energy saving, which given the costs of converting aviation to the new fuel source “I’m not sure it justifies the risk”, says Terwilliger.
However, this rises to 14% if heat recovery alone is used, and to 26% with heat and water recovery – the architecture proposed by HySIITE – which is “starting to open up some daylight in terms of which pathway makes more sense in the long term”.
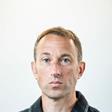