Airbus is nearing several key milestones on its UK-led Wing of Tomorrow programme, with the third fully-equipped demonstrator now in build and the project’s second asset ready to begin destructive load testing.
Wing of Tomorrow is examining a variety of new technologies which could be incorporated into lightweight, low-drag wings, with broader spans and higher aspect ratios, to improve performance and fuel efficiency for a next-generation narrowbody.
It also seeks to determine whether such technologies can be introduced at sufficiently low cost and applied to high rates of aircraft manufacture.
A first demonstrator is in place at Airbus’s wing production site in Broughton, North Wales to “bring together all these technologies for the first time in a real industrial environment…and to really understand if they really meet the targets originally set,” says Sue Partridge, head of the Wing of Tomorrow programme.
That prototype will soon be joined by a sister structure, the programme’s third, which Partridge calls the “run-at-rate wing” – a way of stress-testing the production system to ensure it can support forecast output levels.
“We are now really trying to stress the industrial system, step by step, build each stage of the wing and say, does the industrial system really meet its targets?
“The guys are now in the midst of assembling that run-at-rate wing and testing the industrial system and really, you know, ramping it up to the right level that we planned.”
Last year, Airbus shipped the second wing built under the programme to its facility in Filton in southwest England.
It has since been prepared for test and moved into its Aerospace Integrated Research & Test Centre (AIRTeC) facility.
The 17m (56ft) structure is now attached to AIRTeC’s ‘strong wall’ and Partridge says “[we] are preparing to start testing”, a process due to start by the end of July and to run for around one year before the wing is subjected to its final destructive full-load test.
Tests will check both the capability of the novel composite technologies used and to “make sure we haven’t put any excess strength into that wing so we are not carrying extra weight”, she says.
Data from the testing will also be used to validate a full-scale digital model of the wing, allowing the airframer to move faster on its next programme.
Separately, Airbus is testing the Wing of Tomorrow’s folding wing-tip and its actuation system on another ground test rig.
Sized to add around 10% to the present span, integration of the wing-tip into “quite a complex test system” is under way with the expectation of starting trials by the end of the summer, says Partridge.
In addition, Airbus is hoping to secure funding from the Aerospace Technology Institute – which also backed Wing of Tomorrow – for a project to study engine integration onto the wing.
With the airframer contemplating the use of an open-rotor engine on its next narrowbody, Partridge says Airbus is “now looking at what are the implications of integrating some of those more challenging engine architectures onto the wing.”
In addition to the engine itself “and looking forward to ZEROe” – the manufacturer’s zero-emission aircraft project - “it is also thinking about the integration of a hydrogen fuel system into the wing as well”.
Meanwhile, Airbus is collaborating with GKN Aerospace, Cranfield University and the University of Manchester on another ATI-backed project to advance sustainable high-performance wing technologies.
Called SusWingS, the £15 million ($19 million) project builds on work undertaken in Wing of Tomorrow and is examining technologies including new carbonfibre composite materials and advanced fasteners. Work is already under way and will complete by the first quarter of 2026.
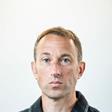