BAE Systems has detailed its progress in producing a supersonic demonstrator in support of the UK’s Future Combat Air System (FCAS) activity, with its critical design review (CDR) completed and build work advancing.
“More than half of the aircraft’s weight, including the fuselage and wings”, are now in build or assembly, the company says. It has released the first images of the demonstrator – being built as part of the UK’s Team Tempest activity – showing its forward fuselage in an assembly jig at its Samlesbury site in Lancashire.
Paul Wilde, BAE’s head of Tempest, highlights the use of new manufacturing technologies, including a Hot Isostatic Press technique, “which uses extreme heat and pressure to create a solid metal part in any required shape” from powdered titanium. In addition to reducing waste during the manufacturing process, this also delivers structures with increased strength.
With the CDR activity having concluded in May, BAE and the UK Ministry of Defence (MoD) used the Farnborough air show to announce that the platform will feature an “integrated payload bay”.
Future test and evaluation work involving the weapons bay – the first to be designed for a British aircraft since the Blackburn Buccaneer – “will be a very important learning for GCAP”, Wilde says, referring to the Global Combat Air Programme between Italy, Japan and the UK. “We are working in collaboration with MBDA to trial digital weapons integration,” he adds.
The first such asset to be produced by the UK since its Eurofighter-precursor EAP of the 1980s, the demonstrator is due to take to the air for the first time by mid-2027.
“Rolls-Royce is set to deliver two [Eurojet] EJ200 engines for installation into the flying demonstrator within the next 12 months,” BAE says.
“Doing this for the first time in 40 years is a challenge, but we wanted it to be a challenge: that is the point of the programme,” says Air Commodore Martin Lowe, the MoD’s FCAS programme director. “We are learning an awful lot from this [demonstrator] programme which is being fed directly into GCAP,” he adds.
Meanwhile, in advance of the demonstrator aircraft even being assembled, test pilots from BAE, Rolls-Royce and the UK Royal Air Force have already “flown” the platform for more than 215h using a simulator at the airframer’s Warton site in Lancashire.
The use of open architecture avionics means test pilots can “fly on a Thursday, and the fixes they suggest are on the rig by Tuesday”, Wilde says.
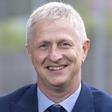