Airbus has hailed the success of an initial round of windtunnel testing using a scaled version of CFM International’s RISE open-rotor engine mounted to a section of wing as part of early aircraft integration studies.
Taking place earlier this year at a facility in Modane in eastern France operated by the country’s ONERA aerospace research centre, the evaluations with the airframer were part of a broader 200h windtunnel programme designed to assess the aerodynamic and acoustic performance of an open-rotor engine.
Airbus says the trials allowed it to “gather high-speed aerodynamic data” – representative of cruise conditions – to “calibrate numerical tools and assess the installation effects on fan performance”.
“The results are very promising, either spot on or exceeding our predictions,” says Frank Haselbach, Airbus head of propulsion engineering.
Airbus has previously announced plans to flight test the RISE engine aboard its A380 flying testbed in the second half of the decade.
Both the open-rotor engine – a Safran design it calls the Ecoengine – and the wing section were at one-fifth scale for the tests.
Haselbach says the windtunnel programme will “evolve” over the next two years, culminating with the engine installed on a full aircraft model.
Tests will be carried out at both the ONERA facility and windtunnels run by DNW – a joint venture between the DLR and NLR, respectively the German and Dutch aerospace research councils.
Although an open-rotor engine promises what Haselbach calls a “massive step in propulsive efficiency”, it also presents significant integration hurdles.
Haselbach, speaking in a CFM-produced video this summer, points to “challenges” including internal and external noise and vibration, and protecting against fan-blade release.
“It is a step-change for the aviation industry to integrate such a motor into a potential new product,” he says, noting that “the aerodynamics of the wing will be challenged a bit by this”.
A recent study by the DLR bears out those concerns. Using a “generic” open-rotor design provided by CFM partner company Safran and a notional Airbus airframe – with a low-wing, high-aspect-ratio configuration – researchers conducted numerical analysis of the simulated installation impact of an open-rotor engine in take-off conditions, assuming an angle-of-attack of around 7°.
The study, conducted as part of the EU’s Clean Sky 2 programme and presented at the AAIA Aviation Forum in July, says “notable angle-of-attack and installation effects were found to effect the aerodynamic performance of both the propulsion system and the airframe”.
These include degraded performance of the swirl recovery vanes (SRVs) – the stator stage aft of the fan – and the generation of “substantial in-plane forces”, also known as 1P-loads, by the rotor and stator, which induce a tendency to make the aircraft roll.
Additionally, the direction of rotor rotation was found to have another impact: affecting the magnitude of the rolling moment caused by the interaction between the propulsor slipstream and the wing and flap.
A rotor spinning with its blades on a downward path when closest to the fuselage was found to create a larger rotational moment, the study found.
“In the interest of ensuring good overall aircraft handling qualities, as well as to avoid the need to trim out the rolling moment these in-plane loads cause, an aerodynamically symmetric aircraft would clearly be preferable, which would mean engines with an opposing sense of rotor rotation on the left and right wing,” the study says.
However, the requirement for the engines to be ‘handed’ – rotating in opposite directions – would have to be weighed against the “likely increased costs this would incur” through the need for direction-specific components such as gearboxes and blades “and the associated spare part and propulsion system maintenance impact”.
Additionally, the study notes certain “unique aerodynamic phenomena” from the interaction of the propulsor slipstream on the wing and flap. In particular, the tip vortices from the swirl recovery vanes offer the potential to “improve low-speed, high-lift performance of the wing and the flap”.
Safran is also leading a research and technology project into an open-fan engine through the EU-backed Clean Aviation programme, a successor to Clean Sky 2.
Called OFELIA – open-fan for environmental low impact of aviation – the objective of the €140 million ($154 million) project is to bring the open-fan architecture to a high technology readiness level by 2025.
This includes a full-scale demonstration of the engine by the end of the project in December 2025 and to “deliver a flightworthy propulsive system definition and prepare an in-flight demonstration” for the second phase of Clean Aviation from 2026 onwards, according to project documents.
“The project will also optimise the engine installation with the airframer and address certification, in close collaboration with airworthiness authorities, taking advantage of the permit-to-fly activity,” it says.
While led by Safran, the OFELIA consortium also includes several European subsidiaries of its CFM partner GE Aerospace, plus Airbus, among others.
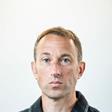