Leonardo Helicopters is close to completing the final assembly of its Next Generation Civil Tiltrotor (NGCTR), as it prepares the demonstrator for a maiden sortie before the summer.
Part-funded by the EU’s Clean Sky 2 programme, the NGCTR development has seen the Italian airframer lead a 25-strong pan-European team since its inception in 2014.
Although originally slated to fly in 2020, delays to the programme – not least from the effects of the Covid-19 pandemic – have seen the target progressively pushed back.
But despite the delays, the milestone now appears in reach, with the tiltrotor taking shape at Leonardo Helicopters’ Cascina Costa headquarters near Milan in northern Italy.
Massimo Biggi, who leads all of the manufacturer’s future fast rotorcraft programmes, says the wing and V-tail were mated to the fuselage in early January, followed by installation of the nacelle structure on the wing-tip, the transmission assemblies and left-hand engine.
Around 95% of the NGCTR’s sub-assemblies or systems are now available for the build, he says, estimating that final assembly will be completed by around end-February.
“I am quite confident that in the next three or four weeks we can show good progress and have a complete asset,” he said in late January.
In parallel, static testing of sub-system assemblies continues, he adds, which “could be the real critical point, because if the test is going wrong that has to be managed somehow”.
But to date, the evaluations have not thrown up any showstoppers. So far successfully completed are aeroelastic windtunnel tests of a section of the wing, with the nacelle and proprotor attached, and of the GKN-built V-tail. Testing was carried out by the DLR and NLR, respectively the German and Dutch aerospace research centres, who are also partners on the NGCTR project.
Meanwhile, static tests of the wing itself are under way at a facility in Brindisi in southern Italy and transmission testing will begin shortly at Leonardo Helicopters’ Yeovil site in the UK using a specially designed rig. This will be used to assess the NGCTR’s transmission tilting mechanism, as well as to perform endurance testing ahead of gaining a permit to fly from regulators.
Around 30h of endurance running will be needed to enable the first flight, Biggi says, with another 20h to be amassed beyond that.
The project’s goal – part of a Clean Sky 2 workstream dedicated to novel aircraft configurations – is to mature five core technologies that could allow Leonardo Helicopters to launch a new tiltrotor for service entry in the 2030s.
“Basically, the five technologies that this demonstrator is testing are the basic building blocks for the future development of the next-generation tiltrotor in the 2030 timeframe,” says Biggi.
As such, while the wing, tail, flight-control system, nacelle and tilting drive mechanism are all new, the fuselage for the demonstrator is a donor structure from the AW609, the airframer’s current tiltrotor programme that continues its slow progress towards certification.
Certain minor modifications were required to enable the integration of the new components and systems, but the biggest change is in the cockpit, where a single Martin-Baker-supplied ejection seat is now installed in place of the AW609’s standard twin pilot seats.
Developed by a consortium called T-Wing, led by the Italian aerospace research agency CIRA, the advanced wing architecture incorporates several key features.
These include a low thickness relative to its chord to increase efficiency, morphing surfaces – principally a large flaperon that rotates to reduce the wing area subject to rotor downwash in the hover – an integrated composite upper skin and spar to reduce weight and simplify production, a curved spar, and a smart fuel system.
If the unswept wing is more an evolution of existing designs, the thermoplastic tail is another story, representing a distinct departure from the T-tail configuration of the AW609.
Biggi says the V shape helps to reduce interference from the wing and trim drag. It should also exhibit “linearity” in its behaviour at high angles of attack, improving “predictability and stability”; a similar design is used on Bell’s V-280 Valor tiltrotor, he notes.
The tilting transmission also has a certain similarity with the V-280. Unlike the AW609, or indeed the Bell-Boeing V-22 Osprey, where the engines and nacelles rotate between horizontal and vertical flight, on the NGCTR it is only the transmission that moves.
Besides offering lower complexity, the fact that the engines remain horizontal means a wider choice of powerplants is available, although for the NGCTR effort twin GE Aerospace CT7s are employed.
As for the fly-by-wire flight-control system (FCS), it features, says Biggi “a scalable, modular and distributed architecture”, which sees the control units for the actuators located together, rather than centrally in a typical federated system. This allows less wiring to be used, helping to reduce weight and complexity, he notes.
Additionally, the FCS gains an active inceptor to improve handling qualities, along with a new human machine interface and bespoke control laws.
Testing of the control system on an avionics rig is under way and should be completed in line with the schedule for the maiden flight: “It is in quite a good shape,” he says.
First to fly the NGCTR will be Gianfranco Cito, chief test pilot on the AW609 programme, who has already undertaken training towards that goal, alongside validation of the aircraft’s “very complex” control laws. “From that point of view, we are very happy,” says Biggi.
Harder to predict though is when that flight will happen. Besides expressing confidence that it will take place this year, Biggi is reluctant to offer a firm forecast. However, he adds: “If we are lucky and everything is going well, in some months we could manage to have the first flight, maybe with some limitations.
“I think in a few months we should be able to fly.” Does that mean by the summer? “Maybe before,” he says.
Once airborne, Cito will progressively expand the NGCTR’s envelope, moving from vertical flight to transition and then wing-borne flight towards its 270kt (500km/h) maximum speed. Ultimately, the intention is to accumulate around 200 flight hours over the next two years, Biggi says.
As you might expect, he demurs when faced with a question on when a follow-on development programme might be launched, simply noting that “it depends on market need”.
Leonardo Helicopters is tentatively proposing a tiltrotor with a maximum take-off of around 11t capable of carrying 25 passengers. The comparative figures for the AW609 are 8t and nine passengers.
It believes such an aircraft will offer significantly lower fuel-burn and emissions than a conventional rotorcraft – it has used the 7t-class AW139 as a reference – alongside wider coverage at higher speeds, while retaining vertical take-off and landing capability.
But such an aircraft could also have a military application, he notes, with Leonardo Helicopters involved in the European Defence Fund-backed EU Next Generation Rotorcraft Technology (ENGRT) project.
Certain technologies developed through the ENGRT initiative are likely to be flight tested on the AW609 and NGCTR, he adds. The separate NATO-led Next Generation Rotorcraft Capability programme may also present a future opportunity to employ the advanced tiltrotor architecture.
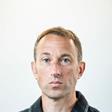