Airbus Helicopters has provided additional details on its plans for the recently unveiled H145-based PioneerLab demonstrator, with flight trials to significantly ramp-up towards the end of the year.
Testing activities will continue through 2024 and 2025, before the helicopter undergoes major modification work to install an advanced hybrid-electric powertrain.
Officially disclosed at the German National Aviation Conference in Hamburg on 25 September, but in development for the last 18 months, the twin-engined PioneerLab is to test technologies to reduce fuel consumption by up to 30%, increase autonomy, and integrate “bio-based” materials.
To date, the PioneerLab has accumulated around 8h of flight time, reveals Tomasz Krysinski, the airframer’s head of research and innovation programmes.
Testing so far has focussed on a rotor-strike alerting system. A similar system was in 2021 evaluated on the airframer’s H130-based FlightLab demonstrator and has now been adapted for the H145.
Krysinski says the PioneerLab is now currently “in lay-up” awaiting modifications to its sensor suite as Airbus Helicopters works to “tune” the system for the larger helicopter.
Later this year, the platform will be used to assess a cable-detection system, which has previously been tested using small uncrewed air vehicles and the FlightLab demonstrator.
Commercialisation of the system could come as soon as 2024, says Krysinski, initially on light-singles such as the H125 and H130, “then we’ll proceed to light-twins”.
However, he cautions: “I’m looking once again in a pragmatic way to have the test results [first] but [commercial availability] will come very quickly just after.”
Next year, flight-test activities will switch to evaluation of an automatic take-off and landing system, alongside other autonomous features, including an active-trim function. Krysinski promises a ”real improvement in the way the helicopter is piloted”.
“We will work for two years on the autonomy functions in a very extensive way. A lot of technologies will be tested and then we will [prepare] the aircraft for hybridisation.”
That will be a major change for the PioneerLab as the modifications required for hybridisation are “quite significant”, he says.
However, Krysinski will not yet reveal details on the hybrid system architecture, or name the suppliers involved.
Airbus Helicopters has previously outlined several pathways for the hybridisation of rotorcraft, ranging from a simple emergency back-up system – a battery and electric motor already tested on the FlightLab – to the hybrid-electric powertrain it plans to fly on the clean-sheet DisruptiveLab as a means to cut fuel consumption.
While the PioneerLab’s hybrid architecture will be “a bit different” to that employed on the DisruptiveLab, Krysinski says it will be used in a similar role: supporting the thermal engines and providing additional power as required, for example during high-altitude operations.
He declines to provide specifics but says the power available from the electrical system on the PioneerLab will be “roughly twice” the 250kW planned for the DisruptiveLab.
On its own, the hybrid powertrain will contribute about two-thirds of the fuel-burn reduction expected from the PioneerLab, with the remainder coming from aerodynamic improvements and lighter components.
Drag reduction activities will focus “especially on the rear part of the aircraft”, says Krysinski, for example focusing on the transition between the rear fuselage and tailboom: “This is really where improvements are still possible.” Changes to the skid gear are another area of potential focus, he adds.
No mass reduction target has been set so far, he adds, as work in this area is still in the “exploration phase”. Similarly, work continues to develop the bio-materials to be tested on the platform to increase component recyclability.
Overall, the PioneerLab programme will run for four to five years as Airbus Helicopters matures the “techno-bricks” on test before any commercial roll-out.
With three Lab demonstrators now flying – two light-singles and a light-twin – is there also a need for, say, a medium-twin-based demonstrator? Krysinski will not be drawn: “It is too early to say,” he adds.
However, with pictures recently emerging of a heavily modified H135 at the airframer’s Donauworth, Germany site, could another light-twin Lab be on the way? Again Krysinski declines to say.
But regardless of specific programmes, Krysinski sees the overall ‘Lab’ concept as hugely valuable: “It helps a lot with our technology development. This is the area where we want to continue going quickly from the idea to the realisation; it’s clearly the way we want to proceed.”
Airbus Helicopters has transformed an existing four-bladed H145 test aircraft (D-HADS), a 2014-built example, into the PioneerLab, in common with its approach to the FlightLab (F-WWXD), which is based on a 2017-built H130 demonstrator. The DisruptiveLab, which is designed to test more transformative technologies, is a clean-sheet helicopter.
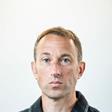