Safran Helicopter Engines is readying key test programmes for 2024 as it works to mature multiple hybrid technologies ready to equip a next-generation engine in the coming decades.
“We are exploring different types of hybridisation – at the end of the day we don’t know which one will take off or be adopted by the market,” says Valentin Safir, executive vice-president, programmes, at the propulsion specialist.
Safran has not yet launched development of a new thermal engine, Safir stresses, but is readying multiple “techno bricks” that could enable hybridisation of that powerplant.
“By the 2030s we want to have different propulsion systems leveraging these different bricks.”
It sees three broad routes to hybrid power, what it refers to as micro-hybridisation, parallel hybrid, and disruptive propulsion.
Micro-hybridisation is essentially Safran’s “eco-mode” for twin-engined helicopters. It is a way to shut down one of the two turbines during the cruise phase – achieving better fuel consumption through running the remaining engine at an optimal power output.
But the crux of the system rests on being able to rapidly reactivate the sleeping engine, particularly in an emergency “where you need a very, very fast restart”, says Safir.
This is where the hybrid element – a small battery and electric motor in the 100kW range – is deployed, enabling a faster restart than would be possible with a standard electric starter unit.
“We don’t need it to power flight for a long time, just to restart the thermal engine very quickly.”
Ground tests using a 2,500shp (1,860kW) Aneto turboshaft were successfully concluded in 2023, showing that an engine restart was capable “within a few seconds”.
Safir declines to say exactly how quickly the powerplant was restarted but adds: “The critical part is that it can be restarted fast enough so that the pilot does not see any disruption to their flightpath. It is much faster than any electric starter today.”
Safran’s next step is to demonstrate the system in flight, a milestone that should take place later this year or in early 2025 using the Aneto-1X-powered Airbus Helicopters Racer.
While the Racer is scheduled to make its maiden sortie in the coming weeks, the eco-mode system will not be evaluated until later in the flight-test campaign.
Safran is also contemplating the path to flight testing its parallel hybrid powertrain aboard a single-engined helicopter having last year completed an initial round of bench tests.
Comprising a battery, electric motor, power electronics and control system, the hybrid system could be used to either provide back-up power in the case of engine failure – potentially for up to several minutes – or to deliver a power boost during certain flight phases, allowing better sizing and optimisation of the thermal engine.
During the first bench tests in 2023 “we learned a lot, especially in terms of [control systems]”, says Safir, with a second ground-test campaign planned “for the second half of this year”.
That will include a simulated failure of the thermal engine and the control system “taking over with electric power” to ensure the flight can be completed safely.
“We need to be able to switch to electric power very, very quickly,” he says. “The control system needs to be ready for that.”
Flight testing remains the end goal and while Safir says Safran “does not have anything to announce yet”, open discussions are ongoing to “extend the development of this system and to test it for real in flight”.
Although Airbus Helicopters has previously tested a battery and motor – what it calls the Engine Back-up System (EBS) – aboard its FlightLab platform, the 100kW EBS provided only enough power for 30s of flight.
Safir sees Safran’s eventual system as being much larger. “We are already talking about a bit more than 100kW [output],” he says. “We are not talking ten times as large, but certainly a bit more than that.”
Ultimately, the system to be developed will be driven by market feedback: do operators want a genuine emergency-only system or a power boost? Safran is seeking to be ready for every scenario, says Safir. “We will keep things very flexible until that point. To choose only one use-case would be too restrictive.”
Meanwhile, Safran continues to prepare the ground for disruptive propulsion architectures – series or parallel hybrid powertrains for vertical or short take-off and landing (STOL) applications.
It has already secured an agreement with US STOL developer Electra that should lead to flight testing of a turbogenerator based on the 1,200shp Arrano helicopter engine.
The system, dubbed the TGen 600, sees a pair of 300kW generators coupled to the Arrano, to generate the 600kW output that Safran thinks will be required across the industry.
A “very successful” ground-test campaign was conducted in 2023 at the manufacturer’s Bordes site in southwest France.
“As a product we have something that is working well. The next step for us is to test it in flight – that’s what we are missing,” says Safir. The agreement with Electra foresees flights within two years, he notes.
Safir says the aim is to add the Arrano-based TGen 600 product to its standard catalogue, potentially in the 2028-2029 timeframe.
But first the system will need to be optimised for size, weight, and output. “The demonstration flight with Electra will be the first step to getting something a bit more optimised and lot more powerful,” he says.
Safran’s goal is to deliver a turbogenerator that is only around 30% longer than the standard Arrano, Safir adds. “That is not what we have but what we are aiming for.”
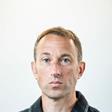