Pratt & Whitney believes the improvements it plans to implement for the second generation of its geared turbofan (GTF) engines could deliver a fuel-burn saving in the region of 25% over current models on an installed basis.
Speaking to FlightGlobal at the Farnborough air show on 22 July, chief sustainability officer Graham Webb gave no timeframe for the introduction of a next-generation GTF noting that it will be paced by the requirements of the aircraft manufacturers.
“But when airframer A, B or E wants to launch a new aircraft… we plan to have the technology ready to provide the solutions they are looking for.”
Planned changes to the GTF – variants of which power the Airbus A220 and A320neo, and the Embraer E-Jet E2 – include a better optimisation of the workload between the engine’s low- and high-pressure spools, the introduction of new lighter and heat-resistant materials such as ceramic matrix composites, and an increase in gear ratio.
That figure sits at around 3:1 at present but this will be pushed to “four and up” for the next version, says Webb. That may also necessitate a shift to a planetary gear arrangement, moving from the current star design.
A larger fan is also envisaged – rising from 81in on the PW1100G to 85-90in on the subsequent generation. Engine bypass and overall pressure ratios will also increase.
Webb estimates that the proposed improvements could generate a fuel-burn saving at aircraft level in the order of 20%. However, an additional 5% gain could also by realised through the hybridisation of the engine – adding electric motor-generators to the high- and low-pressure spools.
P&W intends to validate such an architecture through its participation in an EU Clean Aviation project called SWITCH.
Led by MTU Aero Engines, it combines the German firm’s Water Enhanced Turbofan technology with a pair of Collins Aerospace 1MW electric motor-generators on a PW1100G donor engine.
Collins and P&W have now completed the preliminary design review (PDR) for the hybrid-electric elements of the programme – which also includes motor controllers, high-voltage wiring and batteries.
Geoff Hunt, senior vice-president of engineering and technology at P&W, says passing the PDR milestone means “we’ve really got an architecture we think that’s going to allow us to move forward and start building up that propulsion system.”
Collins proposes to attach the motors to both the high- and low-pressure spools, respectively locating them on the accessory gearbox and in the tail cone. While both are 1MW units, the motor on the high-speed spool is de-rated to 500kW.
However, Hunt cautions that configuration may yet change. “We are studying a lot of different permutations on that; six months from now we may have tweaked it,” he says.
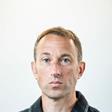